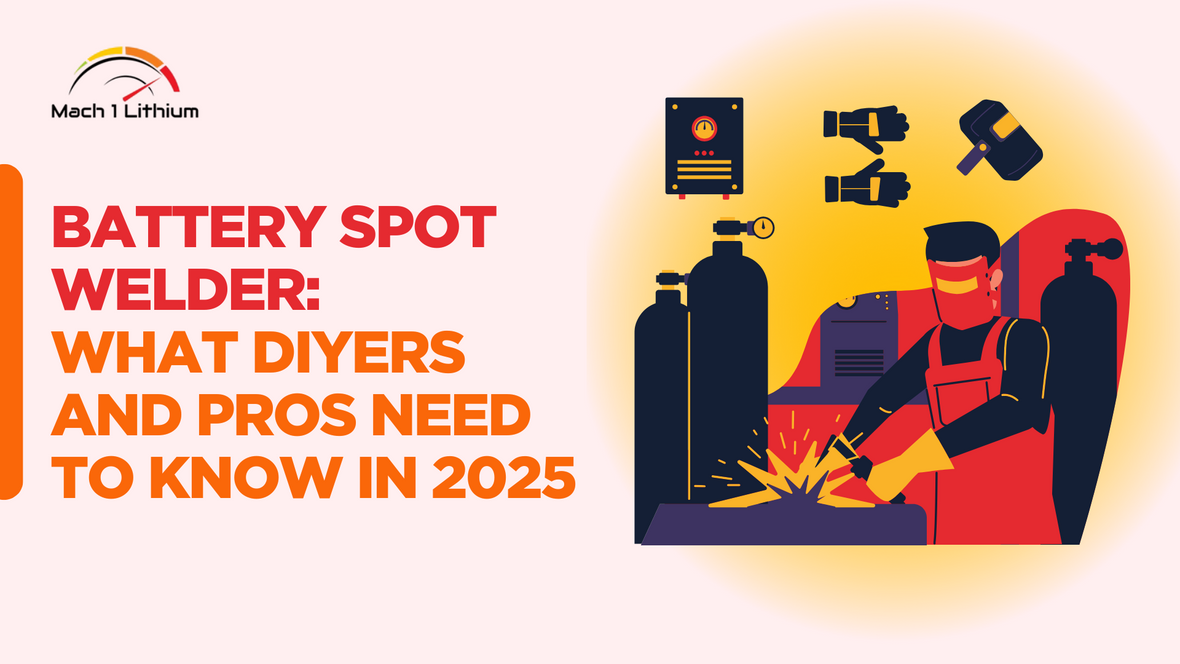
Battery Spot Welder: What DIYers and Pros Need To Know In 2025!
The push toward electric vehicles (EVs) and renewable energy has spurred a massive expansion in battery use. For example, EV sales shares have hit record highs in 2024 (nearly 30% of new cars in the UK were electric), and global battery storage is booming (the U.S. added 11.9 GW of battery storage in 2024, with another 18 GW projected for 2025).
This means more DIY battery packs for e-bikes, home solar storage, and portable power, as well as bigger industrial battery modules. In response, battery spot welders have surged in popularity.
Unlike soldering, spot welding joins cells with a quick, high-current pulse that transfers very little heat to the cells. One instructable notes that spot welding uses “so quick and so localized” energy that “the overall temperature increase in the cell is extremely small”, whereas a 220 °C soldering iron can easily overheat or damage cells. In short, spot welding is faster, safer, and yields higher-quality joints than soldering – a crucial advantage for high-performance battery packs.
DIY vs Professional: Who Is Using Battery Spot Welders?
Battery spot welders are now used by a wide range of people. DIY enthusiasts and hobbyists often build custom battery packs for e‑bikes, drones, power tool packs, and off-grid solar systems.
Making these packs is “a common pursuit” in the maker community; hobbyists routinely salvage 18650 cells from old laptop packs and spot-weld nickel strips to assemble new battery banks. Even simple repairs (rewelding broken battery terminals on tool batteries or e-bike packs) increasingly use handheld spot welders instead of soldering irons.
In online forums, many DIYers report that inexpensive mini-welders (around $40–$60) work for light packs and thin nickel, while serious hobbyists upgrade to more powerful units for thicker cells or larger packs.
On the professional side, spot welders have long been standard in automotive and aerospace manufacturing. Major EV factories use industrial spot welding machines to assemble large-format battery modules. Aircraft and satellite battery systems also use precision welds for reliability.
Even repair technicians – from electric bike shops to electronics refurbishers – are adding spot welders to their toolkits. Quality spot welds are worth the buy even for low-power DIY packs, since a proper spot welder can save time and improve reliability compared to makeshift methods. In short, from garage tinkerers to OEM assembly lines, battery spot welders have become an essential tool for safe, high-performance battery construction and repair.
Spot Welding vs Soldering: The Real Benefits in 2025
Spot welding offers several key advantages over soldering for battery packs, especially by 2025 when high-capacity, fast-charging packs are common. The biggest benefit is minimal heat stress on cells.
Soldering irons run at 200–300 °C, which can degrade a lithium cell’s chemistry or insulation. In contrast, spot welds use a short, intense current burst that “transfers so little heat that the overall temperature increase in the cell is extremely small,”.
This protects the cell’s capacity and safety. For example, heat above 60–70 °C can permanently reduce a battery’s capacity, or worse, above ~100 °C, a cell may vent or explode. Since spot welding confines the energy at the weld spot, the rest of the cell stays cool. (Soldering alone has melted and even detonated cells in maker experiments.)
Another benefit is electrical performance. Spot-welded joints are pure metal-to-metal fusions, which yield very low resistance. In practical terms, a spot-welded pack can carry higher currents with less voltage drop than a soldered one.
Instructables points out that spot welding creates “way lower electrical resistance than soldering, making it ideal for high current applications”. This means more efficient, cooler-running battery packs – important for EV powertrains and high-discharge systems. (By contrast, soldered joints require filler metal, which always adds some extra resistance.)
Finally, spot welds give mechanical strength and reliability. The welded nugget of nickel strip to the cell is robust and vibration-resistant. A solder joint may feel strong because it covers more area, but that strength comes at the cost of heat. As one battery-building blog explains, “a soldered connection is often more physically robust… but the added strength of the soldered connection comes at the cost of lost capacity due to heat damage”.
In other words, the marginal mechanical gain from soldering isn’t worth permanently harming the cells. In practice, spot-welded tabs handle rough use just fine. Many DIYers report that once a weld is done correctly, it holds up even with heavy handling of the pack.

This image shows a battery spot welding process in action, specifically:
-
A pair of weld tips/electrodes pressing down on a nickel strip that's laid across two blue 18650 battery cells.
-
Weld pulse sparks are visible at the contact point, indicating the spot weld is being made.
-
The spot weld joint forms where the nickel strip is fused to the battery cell.
-
A gloved hand is holding the welding tool, ensuring safety during the process.
This setup is commonly used in DIY battery pack assembly, such as for e-bikes, power tools, or solar storage systems.
Industry Trends: What’s Next for Battery Spot Welders?
The battery spot welder market is growing steadily as batteries become ubiquitous. Market analysts project the portable spot welder market alone will reach about $21 million in 2025 (up from previous years) with a compound annual growth rate of 3.8% through the early 2030s. This growth is fueled by demand in EV battery assembly, aerospace, electronics, and even residential solar battery systems. Several key trends are emerging:
- Miniaturization and Portability: New spot welders are more compact and user-friendly. Some models now run from their own batteries, allowing cordless operation. Market research notes, “miniaturization efforts are resulting in lighter, more compact welders, enhancing accessibility and ergonomics,”. Even small bench-top units now often include built-in foot pedals, pistol grips, or handle designs for hobby use.
- Digital and Smart Controls: Modern units increasingly feature microcontrollers, digital displays, and programmable weld profiles. Advanced machines can auto-adjust pulse duration or monitor weld quality in real time. Analysts point out that “advanced control systems with digital interfaces and data logging features are becoming standard in newer models”. Some high-end welders even incorporate AI for adaptive weld control and quality assessment.
- Specialized Alloys & Applications: As battery technology evolves, welders are adapting to new materials. For example, welding thin nickel or advanced copper foil in high-capacity packs requires precise timing. Companies are releasing units tuned for high-strength steel, aluminum, or multi-layer battery tabs.
- Safety and Efficiency Innovations: Greater emphasis on safety is driving features like better insulation, interlocks, and magnetic shielding. Welders with energy-efficient capacitors or optimized pulse shaping reduce energy waste. The shift toward electric everything also means more R&D – for instance, cordless spot welders powered by Li-ion batteries are becoming practical.
Overall, the trend is toward smaller, smarter, and more specialized spot welders. The core need remains reliable, low-heat welds, but innovations are making the tools easier and safer for both industrial and home users.
How to Choose the Right Spot Welder in 2025
Picking the best spot welder depends on your needs. Here are key considerations:
- Portable vs Industrial: Portable spot welders (often running off automotive or LiPo batteries, or wall outlets) are smaller and affordable. They’re ideal for hobbyists or onsite repairs. Their downside is lower power – usually fine for standard nickel strips (0.1–0.2 mm), but they may struggle with very thick tabs or ultra-fast pulsing. Industrial welders (bench-style or armature machines) deliver much higher current (kA-level), and can handle thick steel or copper bus bars. They are bulkier and more expensive, but are required for manufacturing-grade packs.
- Adjustable Power & Pulse Control: Look for welders that let you fine-tune the weld. Adjustable voltage/current, pulse duration, and number of pulses can make a big difference in weld quality. High-end models let you save settings for different materials or cell types. Some even auto-sense the welding gap or thickness.
- Cooling and Duty Cycle: High-current welds generate heat in the electrodes and transformer. Good welders have built-in cooling (water-cooled cables or heatsink tips) and a duty cycle rating. For batch building, a welder with a fan or water jacket can run longer without overheating.
- Safety Features: Make sure the welder has proper grounding, insulated cables, and, ideally, an emergency kill switch or interlock. Foot pedals or hand triggers should be robust. Current models may include indicators for ready-to-weld or error conditions (like “overheat” or “insulation fault”).
- Portability and Ergonomics: If you’ll move it around, consider weight and form factor. The smallest units (like the popular 801B mini-welders) fit in one hand but may have limited output. Larger models (like the 737G+ series) usually sit on a table with a welding arm. Evaluate how you’ll use it – on a bench or in a field workshop.
- Value and Support: Since spot welders vary widely in price ($100–$1000+), balance cost with build quality. Cheaper welders can work for beginners, but reviews often recommend spending a bit more for reliable components (heavy-gauge cables, solid contacts). Check that there is customer support or documentation – a welded cell pack is only as good as the welder’s consistency.
In practice, many users end up with a mid-range spot welder featuring a good balance of power and portability. For example, popular DIY models now come with digital displays and 10–20 adjustable pulse settings, giving home builders professional-level control.
Safety & Best Practices
Spot welding is inherently high-power work, so safety is paramount. Follow these key tips:
- Protect Your Eyes and Face: Always wear safety goggles or a welding helmet. Even though spot welding doesn’t produce a bright arc, bad contacts can create hot sparks or flashes. As one e-bike builder warned, “Always protect your eyes and ears” because sparks of burning metal do fly off the weld. Never look directly at a weld without protection.
- Wear Insulated Gloves and Clothing: Use electrical-insulating gloves or rubber-coated welder gloves to protect hands from accidental contact or hot metal. Wear non-flammable clothing (cotton or wool), as nickel splatter can burn through synthetics.
- Avoid Metal Short Circuits: Keep the work area free of stray metal tools. When welding battery cells, even a small piece of nickel or carbon brush can short a cell. One user recommends wrapping finished sections in non-conductive tape to prevent inadvertent contact. Use plastic or wood jigs to hold cells whenever possible.
- Be Mindful of Pinch Points: Spot welders clamp cells and strips under high force. Don’t put fingers between the electrodes. Keep hands clear of the pinch point and use tongs or fixtures to move parts. (Professional guides note that pinch-point hazards between electrodes can cause serious injury.)
- Check Cell Condition: Only weld healthy batteries. Do NOT weld cells that are swollen, damaged, or have known defects – they can vent or explode under heat. Ensure cells are properly held and won’t shift under the weld clamp.
- Control Electrical and Thermal Risks: Use a well-grounded welder and inspect cables for frays. Never overload the transformer; respect duty cycles. For large welds, allow cooling time between spot pulses to prevent overheating. Avoid touching hot welds immediately after firing, as the metal can be very hot.
- Ventilation: Work in a ventilated area or use fume extraction. Melted nickel and flux fumes can be toxic. For battery packs, ventilation also helps dispel any gas in case a cell vents.
- Common Mistakes to Avoid: Don’t hold the weld longer than needed – excess pulse time just melts through the strip. Don’t press too lightly (you won’t make a good weld) or too hard (you’ll distort the strip). And always test welds on scrap cells to find the right power/pulse settings before working on your actual pack.
User Stories & Community Picks
The battery-building community has many lessons learned. Here are a couple of common insights:
- Upgrading from Cheap Welders: Many builders start with a low-cost spot welder but then move up. One hobbyist reports buying a $40–50 mini welder and finding it just barely adequate: it would tack 0.10 mm nickel fine, but even 0.15 mm strips “was iffy”. He eventually spent an extra $120 on a sturdier welder to reliably join thicker strips. This highlights the trade-off: low-cost units can work for small packs, but more robust welders pay off on bigger jobs.
- Spot Welding Technique: Veteran users stress that weld quality depends on technique. Always start with a clean metal contact (remove cell varnish and dust). One pack builder advises testing your welder on sample cells and listening for a solid “thunk” sound at the tip of the electrode – that usually means a good weld. If you see discoloration or smoke, your settings may be too high. Builders often pre-align strips and press them firmly before welding, and use two short pulses instead of one long pulse to improve consistency.
- Community Recommendations: Online forums recommend a few models consistently – for instance, welders based on 11.6 kW capacitor discharge (like Mach1Lithium’s 801B) are popular among DIYers, whereas brands like Fronius or Panasonic are favoured in industry reviews for heavy-duty use. (See the Mach1Lithium product guide for examples of DIY-oriented models.)
These community experiences underline that spot welding skill grows with practice. Many newcomers suggest building a small 2S or 3S test pack first, to dial in settings and technique before tackling larger batteries.
Why Mach1Lithium Leads the Pack
Among spot welder brands, Mach1Lithium has gained a strong reputation by focusing on innovation and ease of use. Our product line ranges from portable mini-welders to powerful bench units, as “designed for precision and efficiency” to deliver reliable, high-quality welds. For example, models like the 801B and 737G+ offer adjustable pulse settings, durable electrodes, and clear digital interfaces – features that pack builders consistently appreciate. Mach1Lithium also provides clear instructions and support for DIYers, reflecting our commitment to making advanced welding technology accessible.
What sets Mach1Lithium apart is this blend of professional-grade capability with consumer-friendly design. Hobbyists often cite Mach1Lithium’s build quality and performance, for instance, the robust transformer core and ergonomic foot pedal of the 801B, as reasons they trust it for their projects.
Conclusion & Call to Action
Battery spot welding is booming because it solves critical challenges in modern battery assembly. Compared to soldering, spot welding delivers stronger, lower-resistance connections without cooking the cells, making packs safer and more efficient.
As renewable energy and EV adoption grow, the demand for reliable battery packs – and the welders that build them – will only increase.
Whether you’re a weekend DIYer or a professional shop, understanding the benefits and features of spot welders is key. We’ve seen that modern welders offer precise controls, safety features, and even intelligent monitoring to make battery building easier than ever.
When choosing equipment, focus on factors like adjustable power, build quality, and safety. And always follow best practices (wear eye protection, double-check cell orientation, etc.) to avoid mishaps.
If you’re ready to try spot welding for your next battery project, consider exploring Mach1Lithium’s spot welders and resources. Mach1Lithium’s lineup (from the portable 801B to the high-power 737G+) is built with the DIY community in mind, offering adjustable pulse settings and rugged construction for dependable battery pack building.